Already analyzed your data?
From 01.-05.04.2019 we presented our latest Use Case at the Hannover Messe at the booth of the IDS, of which we are a founding member. 2019 was already the second time that we were allowed to participate in the world’s largest industrial trade fair. This year we again presented our work with Telekom. Increased delivery reliability with the help of intelligent data analysis.
What exactly is the project about that Setlog, developed with Deutsche Telekom? To cut a long story short: The aim is to use data science, the right data and years of experience to determine more precise arrival times and thus save costs.
How exactly does this work?
As a provider of supply chain management software, Setlog has been working on optimizing global value chains for over a decade. For our customers we create complete transparency and constantly develop new technologies in order to be able to plan even better and work more efficiently.
Our service is designed in such a way that we cover all of our customers’ processes and present them in our software.
Since 2001, for example, we have accompanied customers from the textile, consumer goods and other industries in managing their entire logistics with OSCA®.
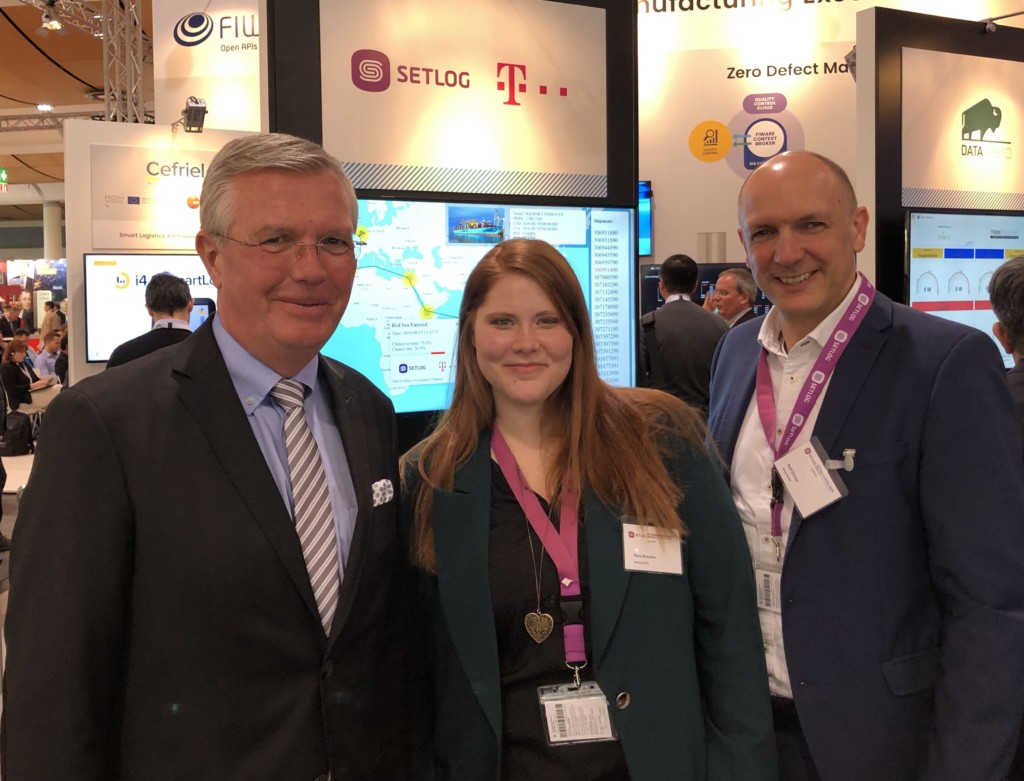
Mostly by ship
The ship is still the most frequently used means of transport. Especially when it comes to goods produced in Asia that have to be transported safely and inexpensively to Europe.
Even if it is the cheapest means of transport, it offers a large target for delays and unreliable delivery dates.
If the goods arrive too late at the port in Europe, this will have numerous consequences.
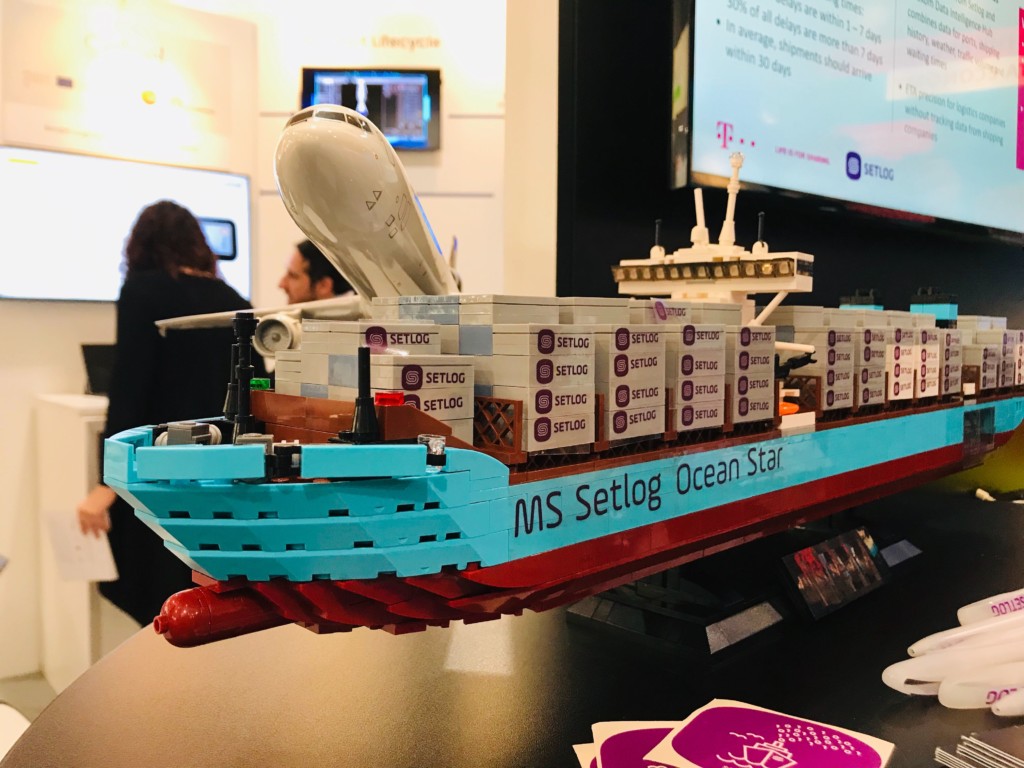
Capacities in the warehouse cannot be used correctly and optimally, costs increase and further planning is strongly endangered. In the worst case, even contractual penalties are imposed.
Our goal: adherence to delivery dates and lower logistics costs.
But how can companies increase their delivery reliability and reduce logistics costs at the same time?
This is exactly the question we at Setlog are dealing with together with Telekom and have been working on the solution for several months now.
This solution was presented at the Hannover Messe at the beginning of April at the stand of the International Data Spaces Associations.
In the “Reduction of logistics costs based on predicted processing times” application case, companies can obtain transport offers from forwarders and immediately compare the different prices with each other. As soon as they have decided on a transport with the freight rates offered, our OSCA® software uses Telekom’s Data Intelligence Hub technology to predict a more accurate estimated time of arrival (ETA).
How is this possible?
With the right data, state-of-the-art technology and data science. To do this, transport data from the past is combined with planning data from the MMS, actual data from OSCA® and publicly accessible data (for example from the areas of traffic or weather), so that the user receives a more precise statement about transport and delivery times.
This results in the following advantages for the customer:
– Shippers can better plan resources and warehouse activities
– More transparency in transport and delivery
– Optimized coordination of all associated processes
– Reduced costs, less time and less resources required
– Avoidance of expensive means of transport such as air freight
– Increase of adherence to delivery dates
– inventory reductions
– Improved cash flow
The Telekom Data Intelligence Hub (DIH), which was presented at the 2018 Hannover Messe, provides the prerequisite for secure data analysis. It is based on the International Data Space (IDS) standard developed under the leadership of the Fraunhofer-Gesellschaft.
Data traffic based on the IDS standard is handled exclusively between a company that provides data and its partners – external or central data storage is no longer required.
The response at the Hanover Fair was consistently positive. Many globally producing companies are only too well aware of the problem of adherence to delivery dates for their transports and are looking for solutions to improve them.
Due to the strong internationality of the trade fair, interesting and fruitful discussions arose which will continue to shape the use case in the coming weeks.
As a special treat, visitors of the booth could not only listen to the advantages of data analysis, but also view a real case study live.
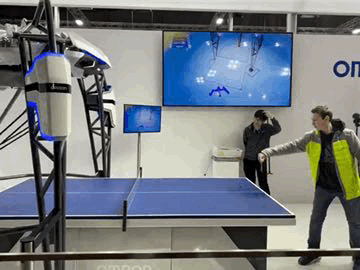
With our tracker it was possible to track routes that container ships had taken in the last few months and, based on data analyses, it was possible to predict the probability of arriving too late or even too early at the final destination.
All in all, the Hanover Fair offers the space for a high degree of interactivity for both visitors and exhibitors – especially with new technologies, the Hanover Fair offers all participants visual and haptic experiences and thus makes the fair a very special event. In any case, we are looking forward to being there again in 2020!