OSCA Quality Control
Never miss another thing in Quality Control

Integrate a holistic process
Fewer quality risks with OSCA
Our QC solution offers optimum quality monitoring of your products. Plan your tests and inspections holistically and track progress transparently for shorter lead times. With OSCA, you not only identify quality problems faster, but also accelerate the flow of information to minimize quality risks!
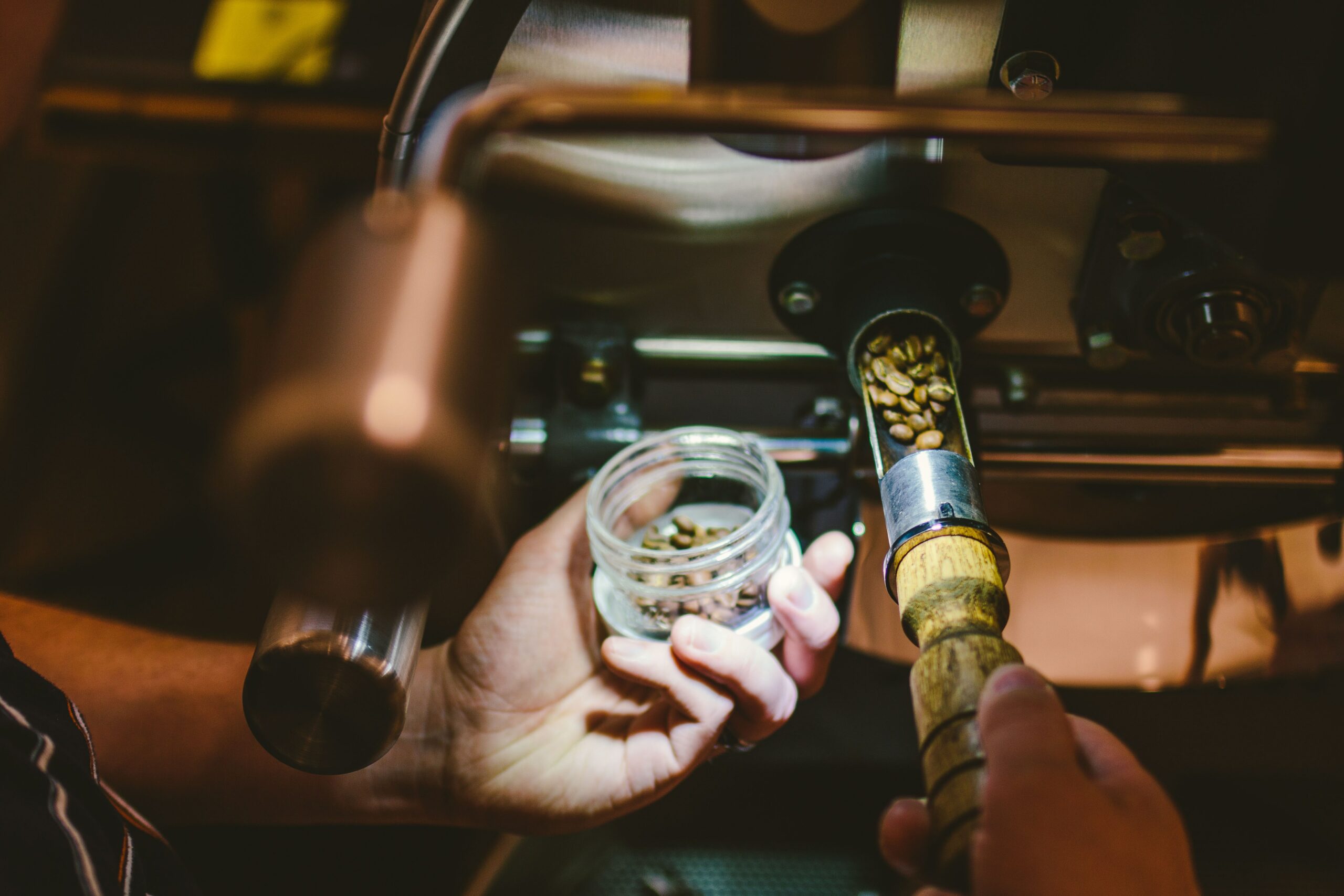
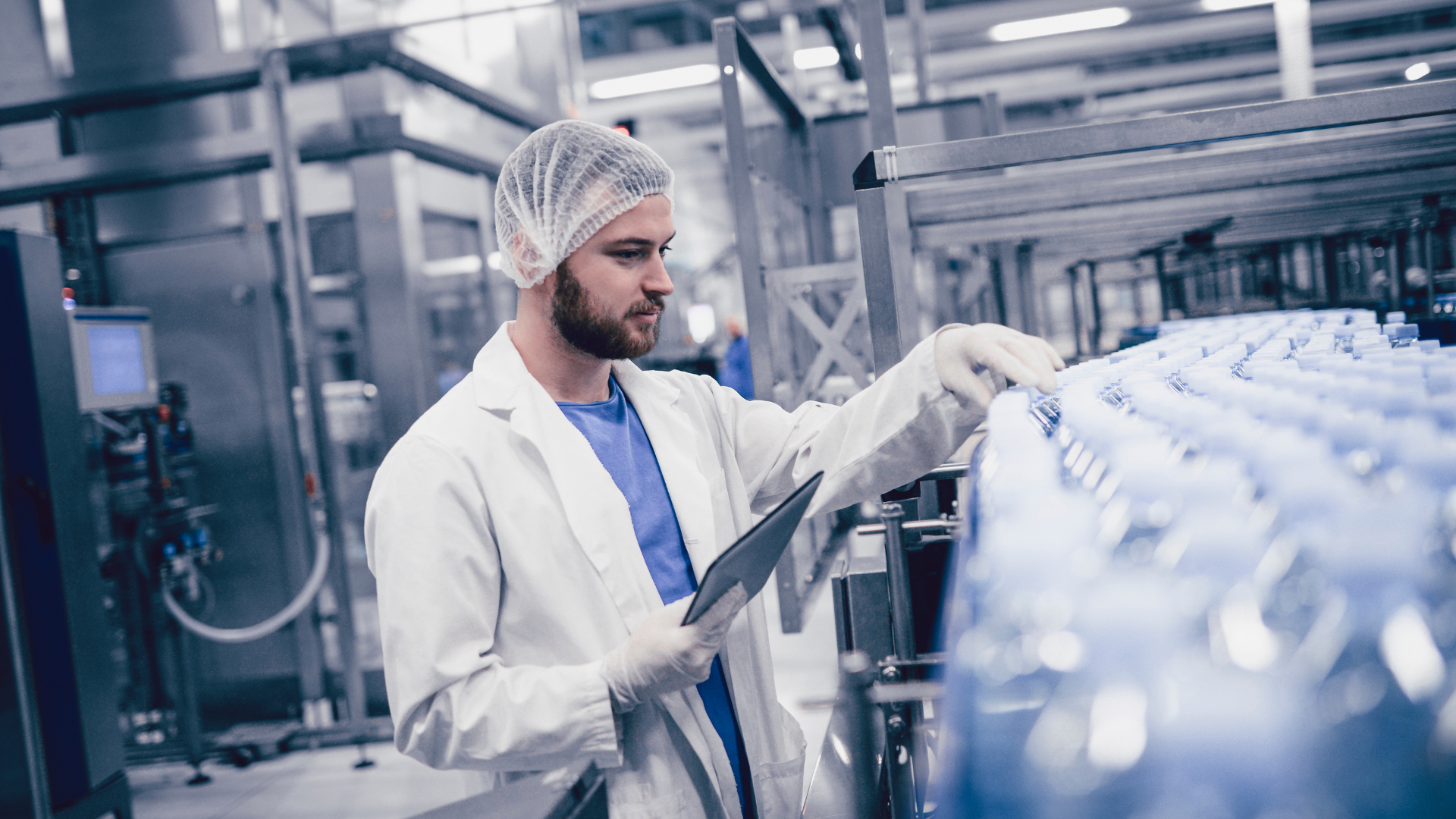
More overview, less effort
Quality management to the point
OSCA always keeps you up to date so that you can react as quickly as possible – with automated notifications and overviews of your new tasks. You can order tests and inspections directly in the system and record the results. In addition, via our system, we connect all partners who are integrated into your quality process directly with each other for centralized communication.
OSCA integrates directly into your processes
We link OSCA with your entire existing IT landscape to ensure that all data from your quality management system flows together.
Import from your ERP or QA system to process predefined inspection lots in the system
Synchronization of test results with the ERP or QS system
Open API structure with other test acquisition or PDM systems
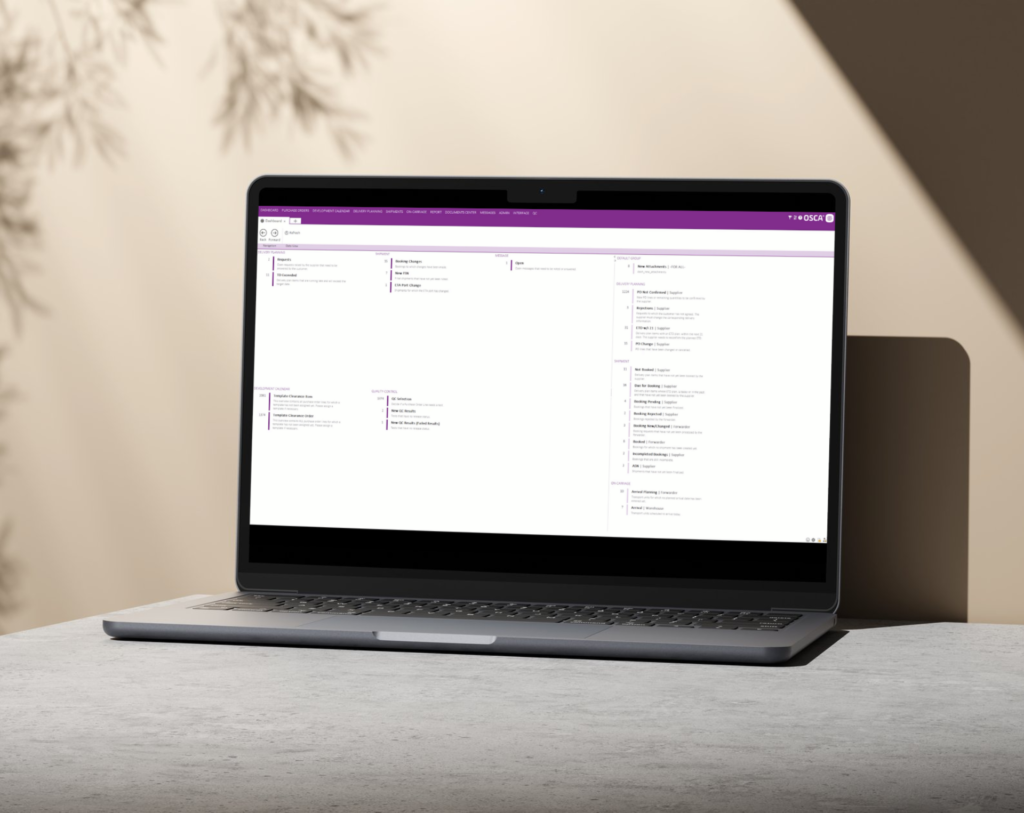
Clothing manufacturer Ospig obtains an overview with OSCA
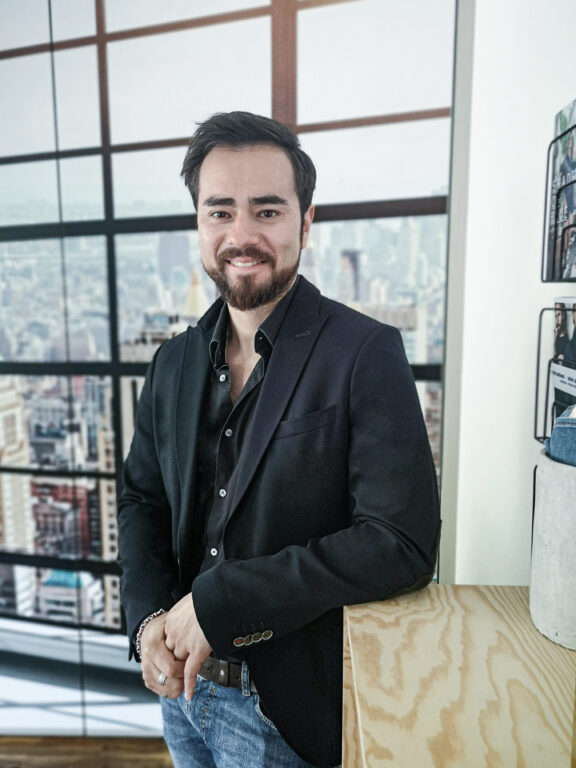
We wanted to get transparency in the value chain and at the same time make sure that all supply chain partners are informed of every change in real time.
Julius Lo, Ospig
Read more about Quality Control:
Get to know us personally!
Make an appointment and find out more about quality control in our system.
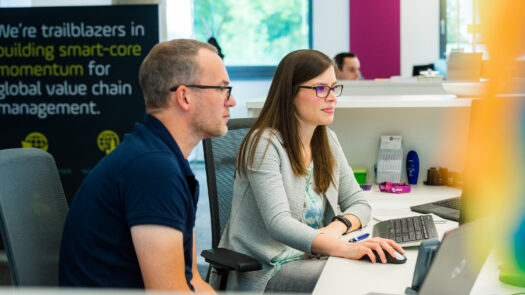
Find us here
Setlog Corp.
420 Lexington Avenue, Suite 300
New York, NY 10170
USA
T: +1 212 209 3969
info@setlog.com
Setlog GmbH
Alleestrasse 80
44793 Bochum
GERMANY
T: +49 234 720 285 00
F: +49 234 720 285 99
info@setlog.com